
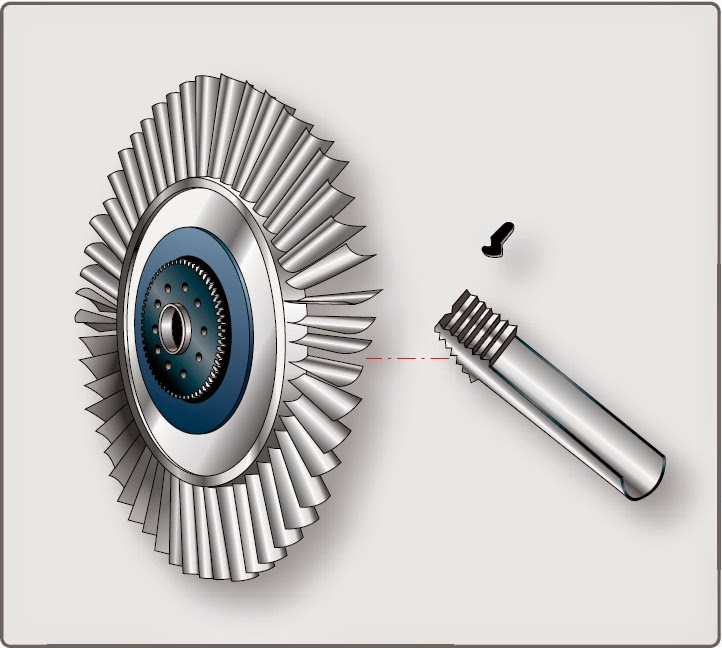
At higher frequencies the smaller skin depth of copper causes the impedance of those bars to increase. As can be seen in the figure, the copper rotor has substantially lower resistance over the whole frequency range, but the difference is largest at running conditions. 3 encompasses not only starting and running frequencies, but also the frequencies of currents in the rotor bars due to the various space harmonics of the stator winding. Our objective here, however, is to discuss ways of designing rotor slots for fabrication by casting a single material, as is commonly done with aluminum as the rotor conductor material.įigure 3: Aluminum and Copper Slot Resistance In such machines it is common to employ 'starting' bars of higher resistivity material. This is often done in large motors in which squirrel cages are fabricated from bars of material brazed to end rings. The use of copper as the conductor of induction motor rotors would typically lead to improvements in efficiency, relative to motors using aluminum. On the other hand, starting torque is lower for the low resistance rotor and this might lead to unsatisfactory performance in some applications. The characteristic curve with higher resistance would, for all load torques, operate at a somewhat lower running speed (and hence higher slip and lower efficiency) than the machine with the lower resistance. speed for two identical notional induction motors, differing only in the value of rotor resistance, commonly noted as R2.

We propose to examine the frequency response of the rotor bar impedance for indications of how the motor will work, taking into account not only running efficiency and starting performance but also stray load losses which are also affected by rotor bar impedance. We employ a simple model that has been developed for this purpose. In order to understand how induction motors work it is necessary to have a good model for the conduction properties of the conductors in the slots of the rotor. In this paper we examine the tradeoff between running efficiency and starting performance. In addition, the reduced losses in such motors may lead to better design flexibility and therefore motors that are more compact. The objective is to make motors more efficient because of the higher conductivity of copper. There has been, in recent years, an effort to make cast copper rotors for industrial use induction motors. Optimization of Motor Rotor: Slot Shape, Frame Size, Rotor Diameter SLOT SHAPE Designing Squirrel Cage Rotor Slots with High Conductivity I.
